Tsugite Bioplastics + Parametrics

- Bioplastic printing
- Generative design
- Parametric design
The endless wellspring of the ISLA project led me down the parametric pathway. The ability to design and print my own product parts, as in my own mini manufacturing facility, is a wonder of our age. This skillset gave me endless Christmas mornings, waking up to the beautiful golden prints designed the previous night. While a bit too much of my time was spent in epic physical battles with the printers, I consider 3d printing to be a marvel of our modern era. From parametric pots to tiny kids toys to tool holders, the results have systematically improved my life.
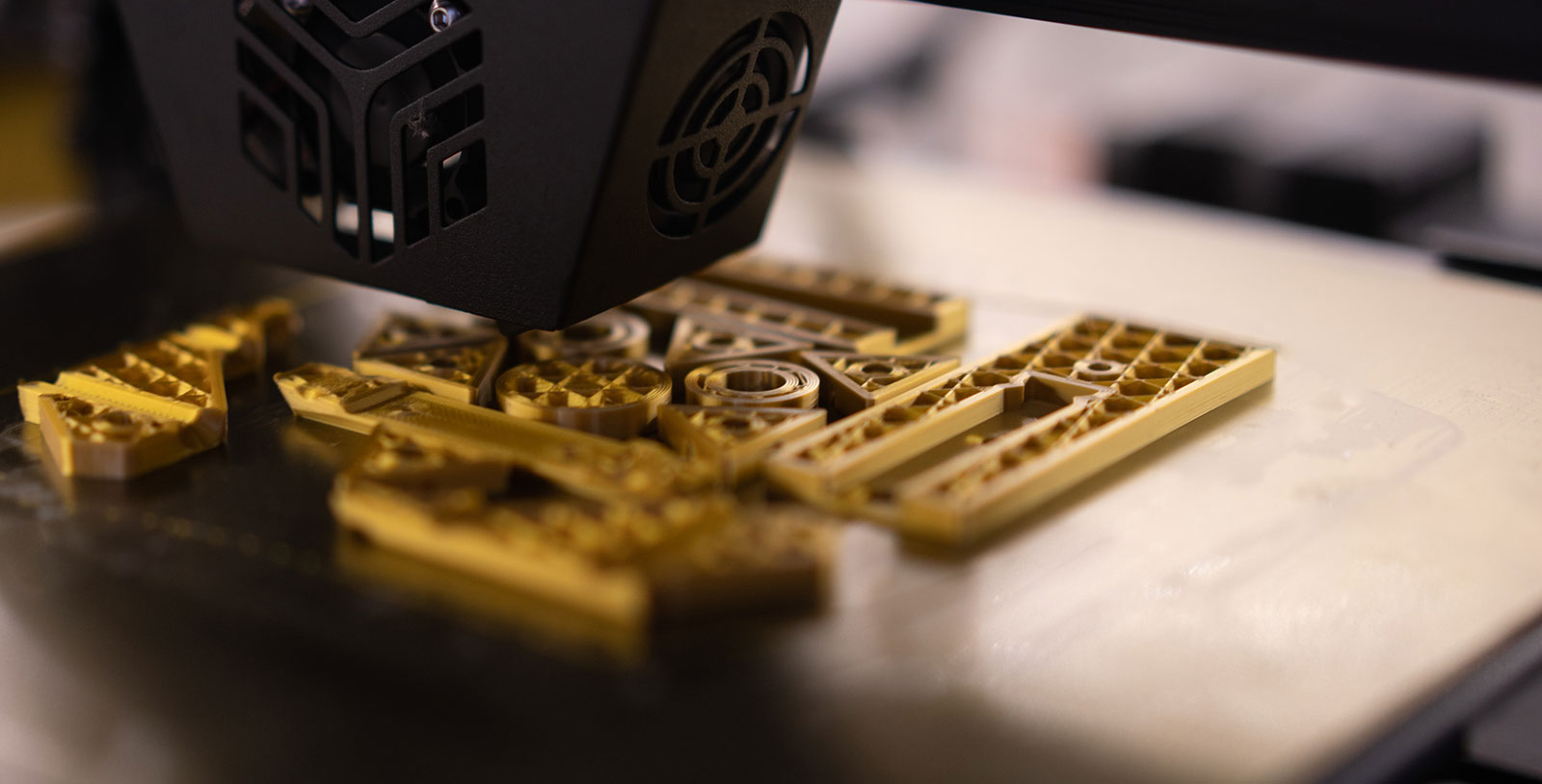
Methods
Fusion 360
Rhino + Grasshoppern
Dual CR6-SE 3d Printers
UltimakerCura
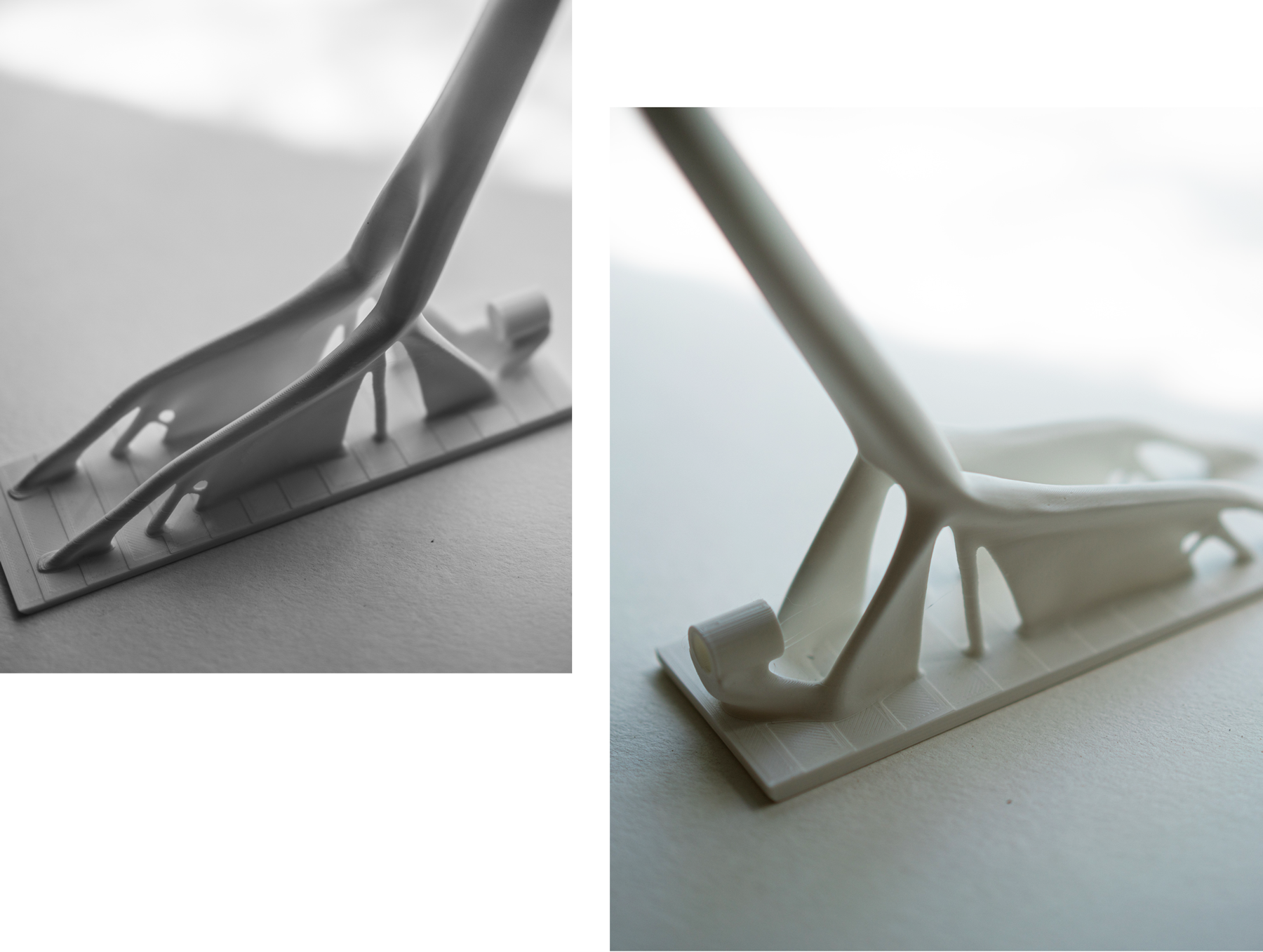
Here is an example of shelving brackets made using generative design, yet another coming revolution. Forces, loads, mandatory sections are defined within CAD software, which then calculates the shape required to give the part a shape with the optimal strength and minimum of material. Parts designed with generative studies have shapes that I find beautiful, organic and sometimes downright alien. This is a current area of study and more studies will be generated in the near term.
Generative Design
Holding Hand
DP sculpture : Study I. Separately printed 3d parts are precision connected by 1mm wire.
Bioplastic Isla parts
Many nights were spent in Fusion 360 making prototype parts for the Isla. "Hot out the oven," the new designs would be ready every morning. Like the process of learning to bake, results became slowly better as experimentation yielded to an exact recipe.
Below are some of the "kanbans" for the Isla. Once all the required parts are taken out of the printer and slotted into its kanban, they are swapped out for empty kanbans. Each Isla requires 9 of these kanban trays of parts.
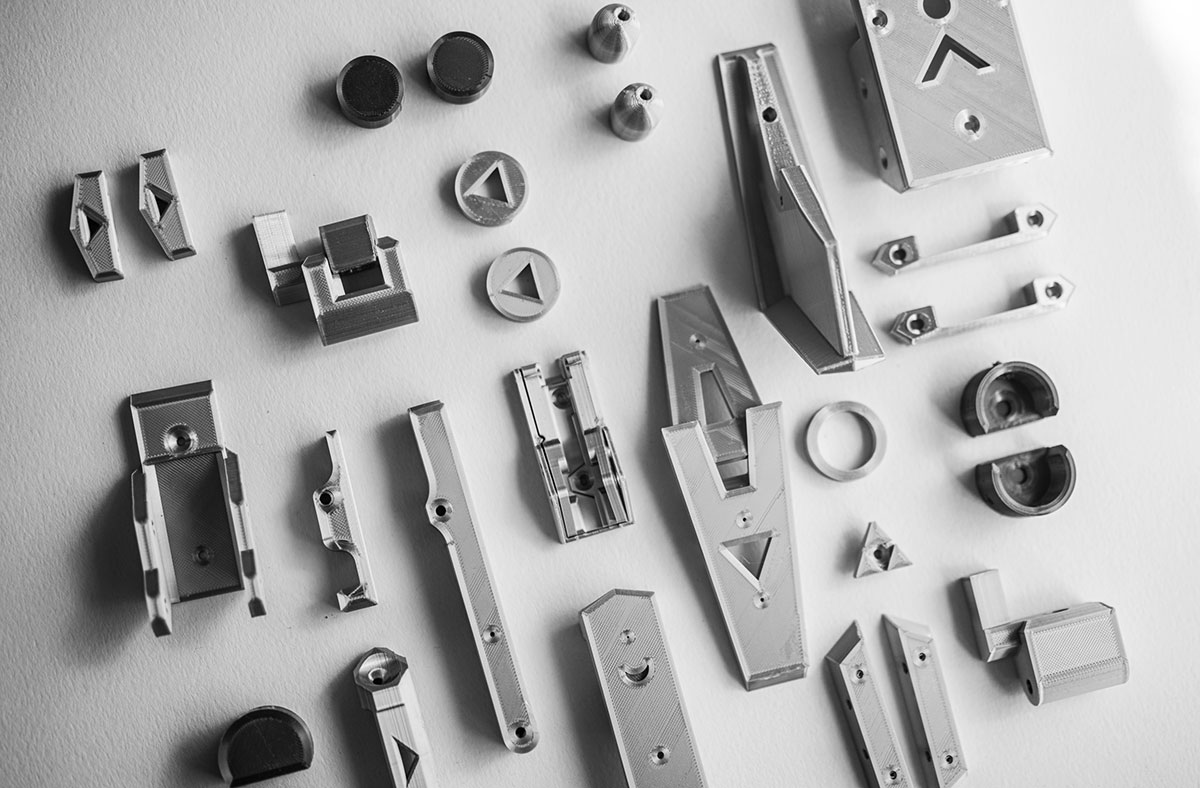
3DP Tsugite Method
Models printed by fused deposition modeling (FDM) have a strong axis and a weak axis. A human figure printed standing up right could split fairly easily along its belt line. This weakness generally renders useless parts that need to cope with multi-axis forces, like hinges. In the quest to make the strongest possible FDM 3D printed part, I developed a method called 3DP Tsugite, named after the tetris connections of Japanese joinery. This script divides a part into 2 or 3 sub-parts, then placed on perpendicular axises to the printing base. Once printed, the sub parts are snapped together (in a most satisfying way). The resulting Tsugite part has no "weak axis", and is up to 8x more durable than a standard part.
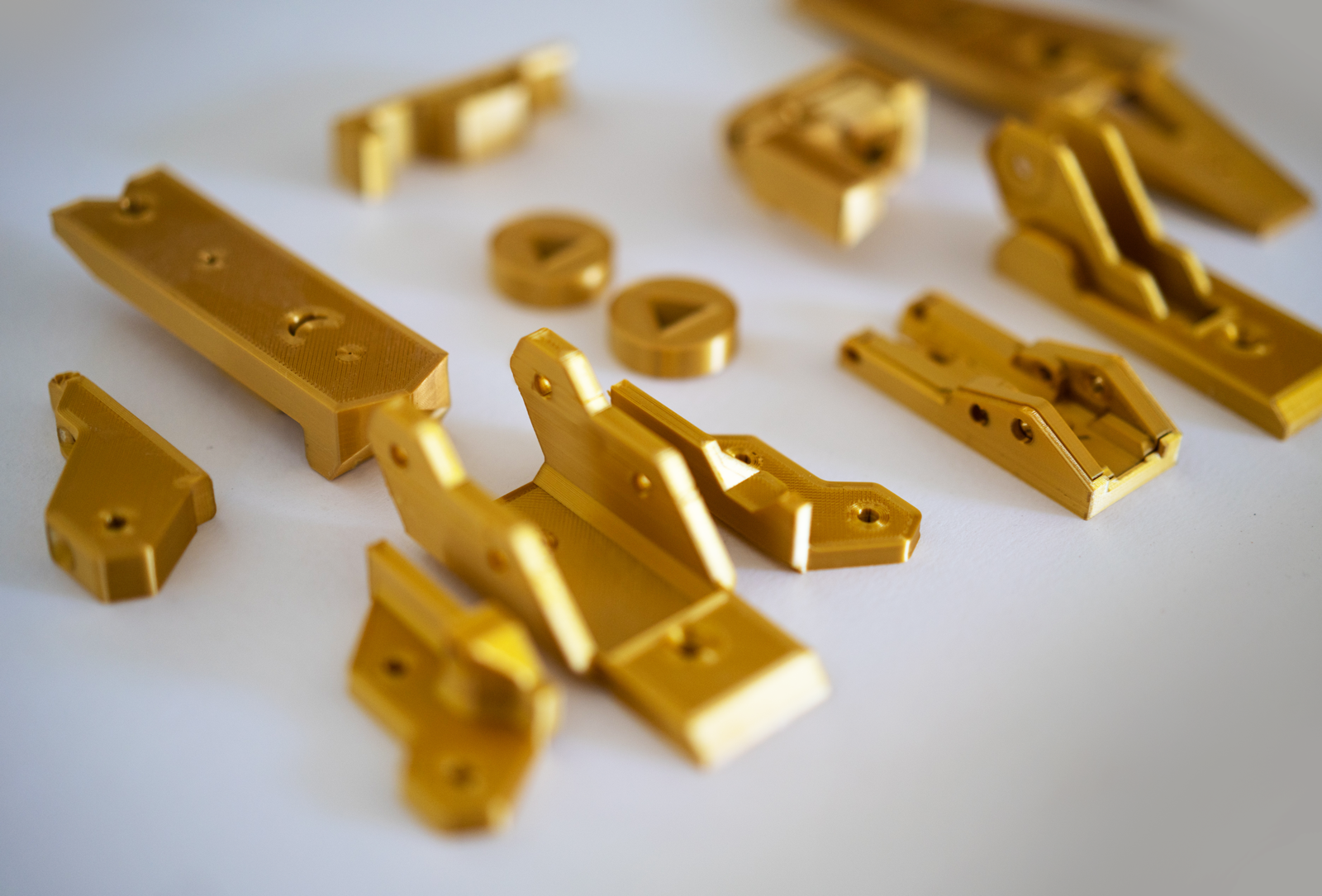